I needed a pipe mounting flange for a project, so I decided to make one and get some experience with lost foam casting at the same time. This flange is used to connect a metal plate to a one inch water pipe. I could have bought a flange, but I wanted to try lost foam casting. First thing to do was to design the part. I used Fusion 360 to do the design.

The mounting holes and the set screw hole are not included here as they can’t be cast. The design was converted to G code for my CNC router. The router was used to make a foam pattern of the flange. I used pink construction foam and machined the pattern out of a 4 X 4 X 2 inch block of foam.

This is an early attempt at machining the pattern. The mistake I made here was using double sided tape to hold the foam block while being machined. The tape gets milled when cutting the rim of the part. The adhesive on the tape sticks to the foam and tears it. Solution is to only put tape where it does not get milled. A neat thing about lost foam casting is that you don’t need any draft on the pattern.

To improve the surface finish the foam patterns and the sprue are coated with thinned dry wall compound. In the above image two patterns are attached to the sprue. The coating was first brushed on then the pattern was dipped in the compound. It is important to not have any bubbles in the compound as the bubble will make bumps on the casting. More patterns could be added to the sprue if needed.

The pattern is then buried in a bucket of dry sand with the top of the sprue exposed. Here I have added a pouring basin to funnel the molten metal into the sprue. The pouring basin is made with petrobond an oil bonded casting sand. The molten aluminum is poured into the basin. The metal vaporizes the foam and fills the resulting cavity.
The first time I tried this was a disaster. I used a plastic bucket which would have been all right except I spilled some of the molten metal which melted the bucket. Sand and molten metal ran everywhere.
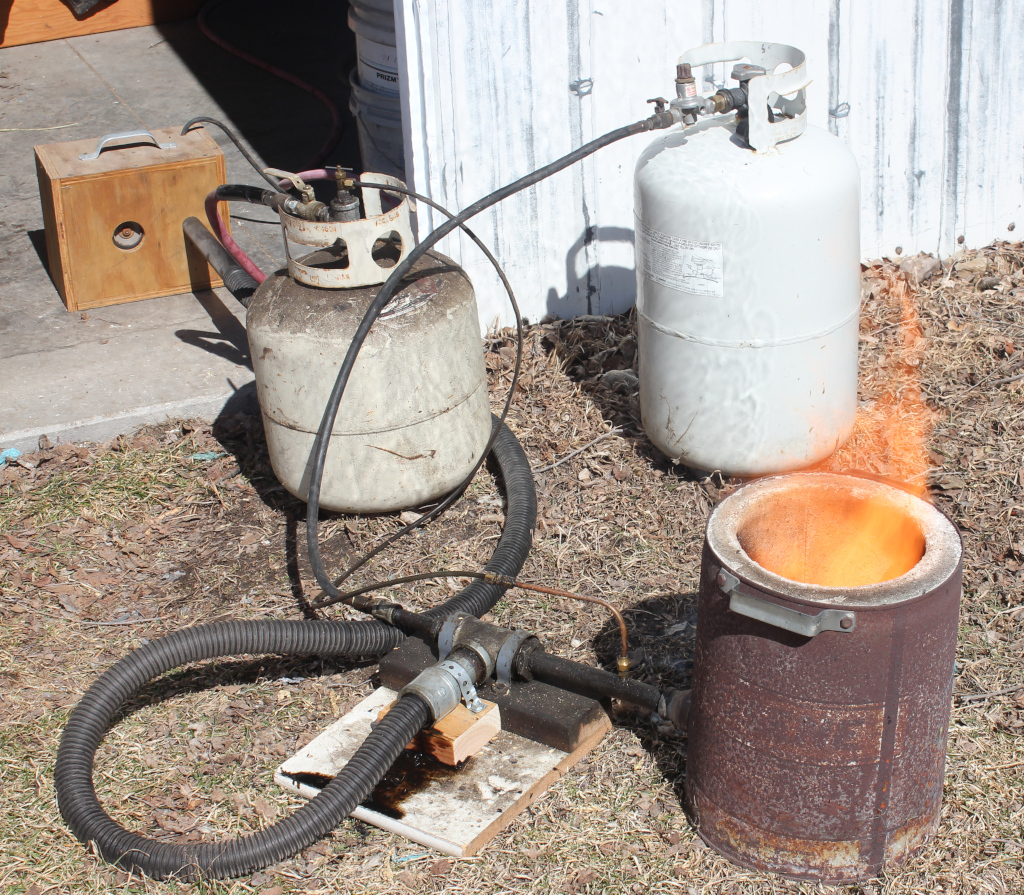
The above image is the setup I use to melt the metal for casting. The furnace is a refractory lined metal bucket. The furnace is started using propane from the larger tank. Once it is heated up the waste motor oil from the smaller tank is turned on. Starting on propane eliminates smoking during warm up. Once it is running on waste motor oil the propane is turned off. A blower in the wooden box supplies air for combustion. In this image the furnace is warmed up and running on waste motor oil.

Above is and image of the completed casting. After casting I cut off the sprue and machined the base flat. Then the holed were drilled and tapped. This flange fits nicely on one inch schedule 40 pipe.